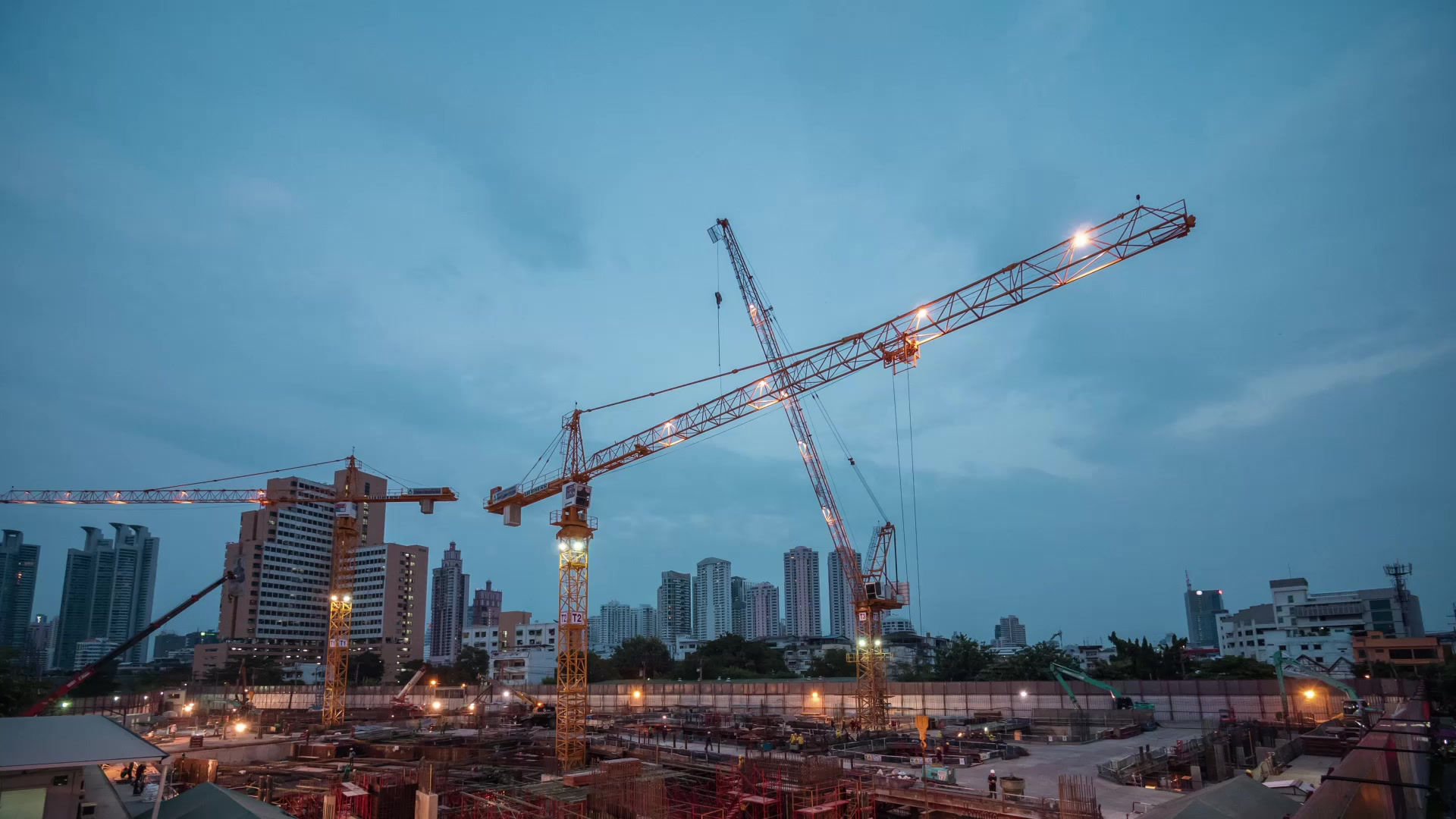
​​
STATION has designed, manufactured and executed architectural precast solutions to various iconic commercial projects throughout the kingdom of Saudi Arabia. Our exterior products are designed in a spectrum of styles, textures, finishes, and shades. This variation adds style and high quality to all aspects of any project. Our processes are always in compliance with international standards, giving confidence to our clients and ensuring best in class development. Our exterior products come in different types of composite materials such as UHPC, Precast concrete, GRC and other fiber-glass producing products that are extremely reliable, resist severe weather conditions and well protected for year-round outdoor use. We work closely with our clients to develop the most cost effective approach to attain their satisfaction and thrive in incorporating quality and aesthetics within their construction requirements.
​​
Type of Composite Material:
​
Glass-fiber reinforced concrete (GRC) is a composite material consisting of Portland cement, fine aggregate, water, alkali-resistant glass-fibers and additives which, when mixed in certain proportions and manufactured under controlled conditions with appropriate equipment, achieves physical properties that allow it to be used for numerous cladding applications, especially those where weight is a significant factor in the design.
Although mix proportions can vary widely, extensive research and industry practical experience has shown that the most typical GRC mix, consisting of a portion of cement, sand, 5% by weight of total mix glass-fiber content, water/cement ratio of 0.33 and a 5% by volume acrylic co-polymer additive, which can produce a composite with significant flexural, tensile and impact strength, provided it is mixed, sprayed, compacted and cured properly.
Advantages of GRC Composite: Aesthetics – Disaster Resistant – Durable – Eco-friendly – Lightweight – Superior Strength
-
Most commonly used on the exterior of structures and a great material for restoration of old buildings.
-
Very popular in the construction industry due to its versatility. It can be cast to any shape and allows the designer more freedom in color and texture than any material.
-
Over several decades it has proven itself to be disaster resistant. Hurricanes, floods, fires and earthquakes are no match for GRC.
-
GRC lasts. It is less prone to weather erosion and extreme temperatures are not a concern on its durability. The use of glass fibers for reinforcement rather than steel means it cannot rust and is reliable to be used in humid environments.
-
STATION GRC weighs about 70% to 90% less than solid concrete. This makes it easier and quicker to erect on site and reduces the load on building structures. The lighter weight and stronger material also saves transport costs, allows more design freedom and, by using less material, reduces environmental impact.
Glass Reinforced Plastics (GRP), also referred to as “Fibreglass”, “Composite Plastics”, and in the USA, “FRP”
The architectural benefits of GRP were accidentally revealed in 1967 with the attempted demolition of Disneyland’s “House of the future”. This innovative house was constructed entirely of fiberglass. When the attraction was considered no longer needed, it was planned for destruction in 1967. It was at that point that the potentials of GRP were recognized. The structure was imperishable. Astoundingly, the wrecking ball merely bounced off the structure. GRP’s use began to increase in the construction industry ever since and by 1995, nearly 600 million pounds of composite materials had been cast-off.
It is a remarkably versatile material, and one that is barely understood in industry, but which has truly vast potential across a wide range of applications. Its enormous range of properties can be puzzling to the unexperienced. It is a plastic but displays hardly any of the shortcomings of conventional thermoplastics in everyday use.
The advantages of GRP / FRP are numerous considering it one of the world’s most adaptable composites. In the construction industry, its application is ideal for domes, vaults, minarets and car parks. It is the product of choice for decorative cladding. In other industries, it is a favored material for boat hulls, bodies and structural components of high-performance cars and aircrafts.
Why GRP?
-
High Strength - It is very strong; seven times the flexural strength of steel, yet very lightweight.
-
Lightweight – Faster installation, less structural framing and lower shipping. High strength to weight ratio.
-
Seamless – Sections can be resined to together to form a single watertight structure.
-
Highly Moldable – Any shape or texture can be produced.
-
Low Maintenance – Indefinite lifespan of the material. Requires no cathodic protection.
-
Durability – Hurricane & natural disasters proof.
-
Aesthetics – STATION molds to meet your specifications and designs. Bronze, wood, stone, iron etc. can all be achieved.
GRG is a molded product with a high strength to weight ratio that is used in construction to substitute the disappearing art of plaster. Plastering is becoming a thing from the past, as very few “Masters” are left. GRG produces better results in a premolded, lightweight, time tested composite for far less the cost. It has been used on probably millions of projects all over the world to continue the charm of both classical architecture as well as creating the free flowing forms of modern design.
Glass-Fiber Reinforced Gypsum is a blend of gypsum, Portland cement, and sand. It comprises mainly of ultra-fine alpha plaster and glass fiber reinforcement. The GRG can then be cast into virtually any shape, and any size. The material is extremely lightweight, and strong, as it requires little to no additional structural support. Glass-fiber Reinforced Gypsum or GRG is intended for interior use only as it not suitable to endure exterior conditions.
GRG, or GFRG, is a building material most commonly used in domes, columns, mouldings and ceilings.
Why GRG?
-
Its low cost, versatility, strength, and lightweight, GRG makes for an ideal building material.
-
The smooth, quality surface provides an ideal base for paint and other finishes.
-
GRG is 100% non-combustible and completely flame resistant. Not only will it not burn, but also safeguard the material behind it from the heat for a substantial period of time.
-
GRG is also painting-grade finish, crack and shrink resistant, and non-toxic. Installing GRG is relatively quick and easy.
-
Glass Fiber Reinforced Gypsum (GRG or GFRG) is a highly durable composite that can be used in a wide range of architectural applications at a much economical cost of other building materials. Whatever the job, GRG can do it rapidly, easily, economically and aesthetically.
Ultra-High Performance Concrete (UHPC), also known as Reactive Powder Concrete (RPC), is one of the latest advances in concrete innovation addressing the limitations of many concretes today. It is an advanced composite concrete material offering unmatched performance. UHPC compositions often consist of a mixture of Portland cement, fine sand, silica fume, high-range water-reducing admixture (HRWR), fibers (usually steel), and water. Small aggregates are sometimes used, as well as a variety of chemical admixtures. Different combinations of these materials may be used, depending on the application and supplier. The use of this material for construction is simplified by the elimination of reinforcing steel and the ability of the material to be virtually self-placing.
The advantages of UHPC are numerous and typically include:
-
Ultra high compressive strength (up to 180 MPa), 2 to 3 times greater than conventional concrete and flexural strength 2 to 6 times greater.
-
Reduced costs such as mould fabrication, labor, maintenance and schedule.
-
Highly mouldable and replicates form materials with extreme precision.
-
Thinner sections and lighter weight than conventional and HPC concrete.
-
Higher quality surfaces and nearly impermeable
-
High Ductility and Volume Stability
-
No steel reinforcing bar cages
The enhanced durability properties have primarily motivated the use of UHPC in bridge applications even in harsh environments. It has also been used in innovative ways to provide new solutions for architectural markets. These applications include bridge beams and decks, solid and perforated wall panels, urban furniture, louvers, stairs, large-format floor tiles, pipes and marine structures.

GALLERIA MALL
.jpg)
MINISTRY OF INTERIOR - RIYADH

PRINCE MAJID TUNNEL - JEDDAH
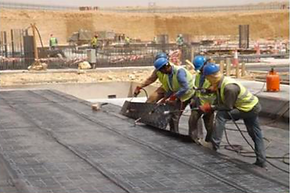
SAUDI ELECTRICITY HQ - RIYADH
PVC - Waterproofing of RCC Wall Sea Side & Epoxy Flooring Works
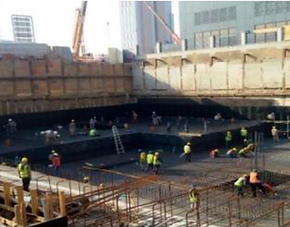
AL ANGARI HOTEL - JEDDAH
This is a Paragraph. Click on "Edit Text" or double click on the text box to start editing the content and make sure to add any relevant details or information that you want to share with your visitors.

RESIDENTIAL COMPLEXES - JIZAN
This is a Paragraph. Click on "Edit Text" or double click on the text box to start editing the content and make sure to add any relevant details or information that you want to share with your visitors.